+40°C the new norm?
10th August 2022
Three days in July 2022 felt an unprecedented heat wave across all of Europe. In the UK a record 40.3°C was recorded at RAF Coningsby, a temperature not felt since the land mass was part of a supercontinent on the equator. It was the first use of an extreme weather warning in the UK where a risk to life is likely.
The days following the event witnessed sweeping statements about the lack of preparation in the refrigeration industry. Design standards are not ready, gas coolers and condensers undersized, adiabatic cooling is needed now, operating pressures need to be increased and so forth. For the first week in August (as I write this article) the temperature is a pleasant 17°C, my allotment has received a (much needed) watering from a rain fall, and the relative humidity is settling around 70%. You won’t find a truer description of a British summer.
So, two weeks after the fact we are back to regular temperatures, systems that failed during the heat wave are back up and running, and the majority of us will look to the next system problem. Probably entrained GWP or leak rates. There will however be some of us, this author included, proclaiming changes need to be made for the next heat wave, and a next heat wave there will be, maybe not this year but the next. It will be more intense and longer than what we have just experienced. Unfortunately, this is the world we have inherited, and the world we must learn to exist in.
What are the solutions on the table?
Raise the working pressures of the gas coolers and condensers.
Pros (other than being able to operate in high heat)
(No obvious benefits beyond operating in extreme conditions)
Cons:
- Compressors work harder
- Higher discharge superheat
- R-744 – Encroaching on pipework high pressure limits
- Refrigerant expands into the vessel with a higher specific enthalpy value
Conclusion
Adjusting existing systems to operate on pressures greater than their design will work but, it demands a change of components including compressors and safety valves. For R-744 systems specifically, KC65 copper pipework will only support a maximum pressure of 120 bar in compliance with regulations, before changing to stainless steel. Overall, making facility for higher pressures on existing and future systems is the ‘over engineered’ approach for a short-term weather event.
Adiabatic cooling
Pros (other than being able to operate in high heat):
- Reduces the air on coil temperature enabling a reduced operating pressure
- Compressor does not work as hard
- Reduced discharge temperature
- Refrigerant expands into the vessel with a lower specific enthalpy value
Cons:
- Increased rate of corrosion on unprepared gas cooler or condensers
- Flora can grow on the equipment
- Additional mechanical system involved
- Water quality control is required
- Questionable use of water if a drought occurs
- Legionella control if required
Conclusion
Beyond the extreme weather events, adiabatic cooling can be used to reduce the air on coil temperature throughout the year, thereby reducing the operating pressure provided, the humidity allows for it (more further down). However, there is a need to install a system fed from the mains water to supply the system. Previous installations have not provided good drainage design which, when on a roof, leads to other problems.
Load Shedding (switching specific cabinets/evaporators off)
Pros (other than being able to operate in high heat):
- Allows the installed plant to operate above its originally designed maximum ambient at the expense of reduced cooling capacity.
Cons:
- Control logic and software needs to be developed and implemented
- Temperature controlled merchandising space is reduced.
- With cabinets, the merchandise will need to be transferred to another case or cold room.
- Only applicable to retailers. Manufacturers don’t have the luxury of shedding part of the manufacturing process.
Conclusion
Load shedding has been explored in the past and has been demonstrated as a method of ensuring the system plant does not trip during high ambient periods. The limitation of load shedding is the reduction of temperature-controlled merchandising space. Fresh produce and beer/wine is not so much of a problem. It may impact the quality/temperature of the product for the period, but they can still be traded. Dairy, no such luck. The goods will have to be removed from the trading period during the load shed. As a retailer this seems like a strange decision to restrict what you can sell but consider, for the few hours where load shedding is needed, the plant is still able to operate, whereas if it failed, all cabinets will have started to gain temperature, all refrigerated product is at risk, a technician will have to be called out to restart the whole system stage by stage. Ultimately, load shedding should be part of any strategy for extreme ambient temperatures.
Discussion
A big driver for adopting adiabatic systems is the ability to retro to existing system to enable them to operate in conditions above their intended design. These conditions come with an additional risk, thus far only mentioned once in this article, and mentioned frequently in the news at the moment. Drought.
Long periods without rainfall have left the UK’s water network at risk of being unable to supply water on demand. A national drought has not been declared in the UK since 1976 but what comes with a drought? Of course, the most important thing water is used for is a drink. We cannot survive without it. As a drought becomes more severe, specific uses of mains water are banned such as hosing a garden, filling a pool, washing cars, even regular washing can become restricted all to preserve the access to clean, safe drinking water. During such an event, the use of adiabatic systems is likely to be restricted but this depends on the regional drought plan. If restrictions are in place, then the system will have to operate ‘dry’ and we could be back to square one. This is of course an extreme example, but such examples should be considered when investigating technology. The what if questions need an answer.
As highlighted in the load shedding section, it is only applicable to non-manufacturing and the lesser of two evils. It can and should still have a place in the retail market by increasing the resilience of the system plant. If used alongside adiabatic cooling, the load shedding will not need to be called on as frequently.
In the UK then, adiabatic cooling is the logical approach to the issue. Yes, existing systems can be retrofitted with new components and pipework rated to the higher working pressures, and yes, new systems can be designed to the extreme temperatures of 40°C. But this level of engineering for a low frequency event (0.8%) is absurd in this authors opinion when adiabatic cooling systems can be retrofitted or installed with new systems. The major cons of adiabatic systems can be mitigated through good design and maintenance practices. However, there are several limitations that must be acknowledged when considering installation. These are the limitations of thermodynamics.
Psychrometry is the field of engineering concerned with the physical and thermodynamic properties of gas-vapor mixtures and it must be understood to know how adiabatic cooling systems work.
We’ve all heard the word humidity. We notice a particularly humid day by feeling ‘clammy’ and warm, like our body temperature regulation isn’t working right. It is, but not as easily. Humidity represents the quantity of water vapour present in the air. A 100% relative humidity means the air cannot hold any more water vapour and evaporation stops. In such an environment your sweat will not evaporate.
Specific humidity is a slightly different metric. It is specifically the ratio of water mass per kilogram of dry air. If we have a body of air with a relative humidity less than 100%, a water source will evaporate increasing both the relative and specific humidity. As these humidity’s increase the temperature of the mixture reduces. The temperature will reduce as far as 100% relative humidity will allow. This is the ‘wet bulb’ (WB) temperature[1]. As opposed to ‘dry bulb’ (DB) temperature. WB temperature will always be lower than DB temperature if the relative humidity is less than 100%. When relative humidity is 100%, the WB temperature is equal to the DB temperature. The lower the humidity, the lower the WB temperature is, the lower the temperature an adiabatic system can achieve. However, if the air is 100% humid, the adiabatic system will have no effect.
For the UK’s now record-breaking example of 40.3°C, I know the humidity at the time was 16% (this is recorded alongside temperature readings) and therefore, a WB temperature of 20.6°C (I will save you the mathematics). That is a significant temperature reduction and would bring a R-744 system back to sub-critical operation. That is provided the adiabatic system has a contact factor of 1, meaning the air after the water system is fully saturated, 100% humid. Unfortunately, in the real world, the contact factor is never 1, and it must be measured empirically. For different contact factors, see the below table:
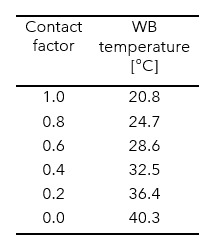
Even without a perfect contact factor, the temperature reduction is impressive, and will greatly aid the operating conditions of refrigeration systems during the extreme temperature events of the future.
WAVE can provide the insight needed to understand how an adiabatic system can help your operations including the energy consumption impact to your design, and prepare for the extreme conditions which unfortunately, appear to be the new normal.
Further reading